Nabertherm is renowned
as one of the leading companies in the branch for almost 50
years.
GERO is established
in the market as a manufacturer of technologically sophisticated
furnaces with application temperatures of up to 3,000°C.
The sintering process is a major step in the production of
technical ceramics. Controlled atmospheres and temperatures are
necessary to create homogeneous textures. Tailor made furnace
design is essential to manufacture high quality ceramic
components.
Nabertherm and GERO
offer a range of high temperature furnaces with the following
features:
- chamber, hood, shaft and tube furnaces
- temperature range from 300 to 3000°C
- volumes from 1 to 20,000 litres
- gas sweeping (nitrogen, oxygen, argon and hydrogen)
- vacuum systems for as low as 10³ bar
- special furnace insulation for aggressive media
- catalyst to decontaminate exhaust gases
- switchgear from program control to all automatic operation
control
- multizone control for temperature gradients of ±1K
The following gives a selection of Nabertherm
and GERO sintering
furnaces:
1. Chamber Furnace HT 160/16/S3
The chamber furnace HT160/16/S3 (Fig. 1) is designed to
manufacture ceramic components at 1,600°C. Gas sweeping allows
sintering in controlled atmospheres. A magnetic door lock
prevents the furnace from opening while in operation. 2 program
controllers operate redundantly. i.e. in case of failure of the
main controller, the sintering process is automatically
continued by the safety controller.
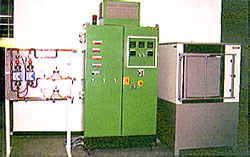
Fig. 1: Chamber Furnace HT160/16/S3
(Nabertherm)
2. Hood Furnace HT64/17/LTS
The HT64/17/LTS (Fig. 2) is used for sintering oxide ceramics
at a temperature of 1,750°C. Four-sided heating guarantees
extremely good temperature distribution. Fast heating and
cooling and low heat loss is provided by insulation made of
high-quality vacuum thermoformed Al2O3-fibre plates. A thyristor-controlled
switchgear guarantees a consistent temperature accuracy of ±2K.
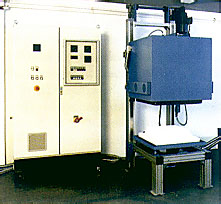
Fig. 2: Hood Furnace, HT 64/17/LTS (Nabertherm)
3. Chamber Furnace HTZ 01/20
Nabertherm is able to offer a chamber furnace for a maximum
temperature of 2,000°C in oxidising atmospheres (Fig. 3). The
outer chamber is heated by 4 Kanthal-Super elements. The inner
chamber with a volume of 1 litre is zirconia insulated and
heated by 4 zirconia elements. Both chambers are controlled
separately and follow fixed heating and cooling rates.
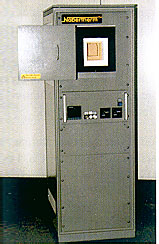
Fig. 3: Chamber Furnace HTZ01/20 (Nabertherm)
4. Chamber Furnace HT 276/17
The chamber furnace HT276/17 (Fig. 4) is designed to sinter
oxide ceramics at 1,700°C. The furnace is equipped with a
warm-air inlet (fan and heater) to guarantee excellent
temperature distribution and to transport the outgoing binder to
the catalyst. The furnace has doors on both sides for easy and
comfortable loading.
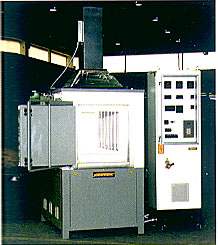
Fig. 4: Chamber Furnace HT 276/17 (Nabertherm)
5. Hood Furnace HT 180/17/LTS
The furnace is equipped with a moveable hood and two
electrically moveable tables (Fig. 5). In a useful volume of 180
litres, oxide ceramics are sintered at a temperature of 1,700°C.
Continuous charging and utilisation of stored heat result in
economical and efficient production cycles. The switchgear is
equipped with a control system to control all electrical
movements. Four-sided heating by 23 Kanthal-Super elements
provides excellent temperature distribution. To increase the
cooling rate, the hood is lifted gradually from 1,100°C on.
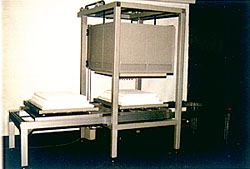
Fig. 5: Hood Furnace HT180/17/LTS (Nabertherm)
6. Shuttle Kiln W1260/14/S
The shuttle kiln W1260/14/S (Fig. 6) was designed with the
requirement that the charge of thin-walled ceramic tubes should
be free from shock or vibration. Therefore, the furnace was
designed for moving on rails while the table remains fixed.
Production takes place in three similar furnaces of 1260 litres
at 1,340°C. Five-sided heating and four-zone regulation
guarantee excellent temperature distribution.
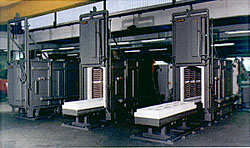
Fig. 6 Shuttle Kiln W1260/14/S (Nabertherm)
|
|
7. Shuttle Kiln W10800/HS1
Ceramic grinding wheels are manufactured at Slip Naxos of
Vastervik/Sweden at a temperature of 1,340°C. The production
takes place in six shuttle kilns W10800/HS1 (Fig. 7).
Five-zone-regulation provides extremely good temperature
distribution in a useful volume of 10,800 litres. A programmable
cooling fan in combination with automatically driven vapour vent
flaps results in short cooling terms.
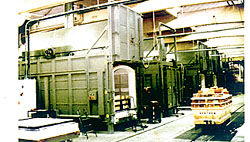
Fig. 7 Shuttle Kiln W10800/HS1 (nabertherm)
8. Hood Furnace HT1010/17/LTS
The HT1010/17/LTS (Fig. 8) is designed to manufacture thin
walled tubes made of oxide ceramics. At a temperature of 600°C
the binder is burned-out and subjected to catalytic afterburing.
The sintering process takes place at a temperature of 1,700°C.
30 Kanthal-Super elements guarantee temperature distribution of
±5K in a volume of 1010 litres. Due to a specially constructed
base, the furnace can be charged with a load of as much as 1200
kg/m².
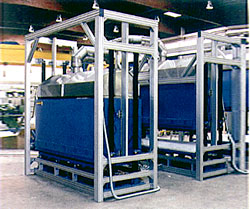
Fig. 8 Hood Furnace
HT1010/17/LTS (Nabertherm)
9. Hood Furnaces N352/AS and HT352/17/LT
The forced-air oven N352/AS and the high temperature furnace
HT352/17/LT (Fig. 9) are designed to burn-out the binder of
oxide ceramics at 600°C and sinter the material at 1,700°C
without unloading the bogie. Four-sided heating guarantees
temperature distribution of ±5 K in a useful volume of 352
litres.
10. Hood Furnace HBO/400
The HBO/400 (Fig. 10) can be operated under vacuum or
non-oxidising
atmospheres at a maximum temperature of 2,000°C. Insulation and
heating elements are made of graphite. Charging occurs from
above when the hood is raised. Dornier at Immenstaad/Germany
uses the HBO/400 for manufacturing fibre reinforced ceramics.
The chamber is evacuated and swept with nitrogen twice in order
to obtain an inert atmosphere. Temperatures. evacuation, gas
sweeping and hood movements are controlled automatically.
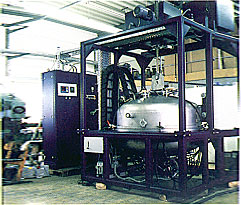
Fig. 10: Hood Furnace HBO/400 (GERO)
11. Ten Zone Tube Furnace ZZ200-2000
The ZZ200-2000 (Fig. 11) is designed for heat treatment of
ceramic superconductor materials. During 3 heating periods of 40
h each, 2000 mm long wires are tempered at 830°C. Due to a ten
zone regulation, temperature distribution of ±0.5 K can be
attained.
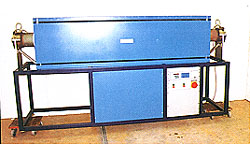
Fig. 11: Ten Zone Tube Furnace ZZ200-2000
(GERO)
12. Tube Furnace BKZ 20-500/5
Hoechst AG at Frankfurt/Main, Germany uses the BKZ 20-500/5
(Fig. 12) to produce ceramic superconductor materials at a
maximum temperature of 1,500°C. The zone melting process
requires extreme temperature gradients to ensure that only a
small area of the speciment is liquefied. This offers the chance
to grow monocrystals without changing the specimen's shape. The
plant is fibre insulated and heated by Pt-Rh heating elements.
The vertical five-zone tube furnace moves at 1 mm/h over the
bar-shaped specimen (10 mm in diameter). The middle heating zone
provides a power of 120 W over 20 mm length which leads to a
temperature gradient of 140 K/cm.
Fig. 12: Tube Furnace BKZ 20-500/5 (GERO)
13. Hood Furnace HBO 250
The HBO 250 (Fig. 13) is used for tempering ceramic
superconductors for 40 h at 800°C in a pure oxygen atmosphere.
With assistance of a centric heating section, a temperature
gradient of ±1 K is not exceeded even during heating and
cooling periods. Due to a mobile, high temperature cone made of
heat resisting steel, a cooling time of 4 h can be reached.
Fig. 13: Hood Furnace HBO 250 (GERO)
14. Microwave Sintering Plant
Using microwave for sintering ceramic components is still
new: The direct application of energy into the material allows
fast and homogeneous heating. Microwave sintering causes smaller
grains, bitter material properties and lower sintering
temperatures.
GERO is developing, in cooperation with the Institute for
Plasma Research (IPF). Stuttgart, a production plant of 500
litres volume for sintering silicon nitride and alumina
components. A plant of 40 liter is already in operation at a
working frequency of 28 GHz (Fig 14), The production plant will
allow a process temperature of up to 1,700°C and can operate at
2.45 or 28 GHz.
Fig. 14: Microwave Sintering Plant
|